

Each motor is equipped with an integrated encoder that can be used to determine the current position of the motor. There are four motor ports on the EV3 labeled A, B, C, and D.
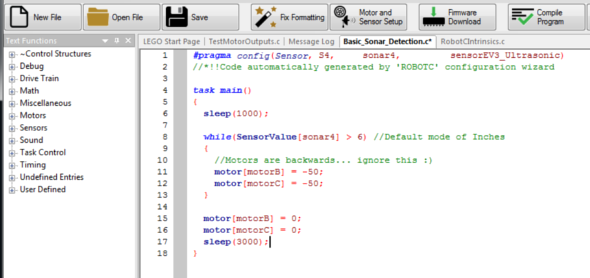
Our Function Library (Updated Spring 2013) EV3 - Motor Commands
#Robotc encoder programming code#
Make the code that converts distance into counts into a function that can be reused. Modify the example to move a selected distance in feet. The number of counts to a unit of distance will be a function of wheel size and the gears used between the motor shaft and wheel shaft. You can also measure the number of encoder counts that translate to actual distance in inches or feet and then set your movement in those units, converting to counts. In practice, you can determine the number of encoder counts needed to complete a movement experimentally by displaying the counts reported by the motors and manually moving/driving the robot through the movement. Demonstrate your program using encoder counts. Having the motor stop automatically is more accurate.Ĭreate a new class called DriveWithEncoder and copy/paste the example code. As shown in the example, you can monitor encoder counts yourself and decide when stop instead of having the motor do it automatically.

Running without encoders just means the motor will take no automatic action, but the encoder is still counting. If your program calls for you to run your motors without using encoders after you use encoders, you must set the motors to run without encoders using the enum DcMotor.RunMode. When you set a speed level, the motor will adjust it's power to maintain a constant speed, to the extent there is battery power available to accomplish that. When you set a power level, the speed of the motor will be influenced by the battery power level and will slow down as power fades. You set the percentage just as you do with percentage of power using the setPower() function. RUN_WITH_ENCODER tries to run the motor at a constant speed, which is a percentage of the max speed of the motor. Run mode RUN_WITH_ENCODER does not stop on it's own. In either case, since we selected the motor run mode as RUN_TO_POSITION, the motor will stop on it's own with brakes on. You could also determine the amount of time needed to complete the movement and wait for that time to pass. The example shows two ways to do that, one watching the DcMotor.isBusy() function (true while motor has not reached the target) and the other compares the current motor position to the target position. Our code needs to wait while the motors are running to the target position. Note we still need to set power to zero when the movement is done. Nothing happens until we set the power level on the motors, then they start running and will run until the encoder count reaches 5000 and then stop on thier own. We set the target position of 5000 encoder counts. Each type of encoder will have a different counts per revolution value so you need to consult the specs for each encoder you use to determine the number of counts per revolution (if needed for your application). A US Digital E4P encoder (in the Tetrix kit) will report 1440 counts for one revolution of the motor shaft. Note that encoders don't count revolutions directly but count partial rotations to allow you to process small movements. You will need to add encoders to both of the drive motors. Then we will run backwards to zero encoder counts to the starting point. In the example code we will run forward for 5000 encoder counts and stop.
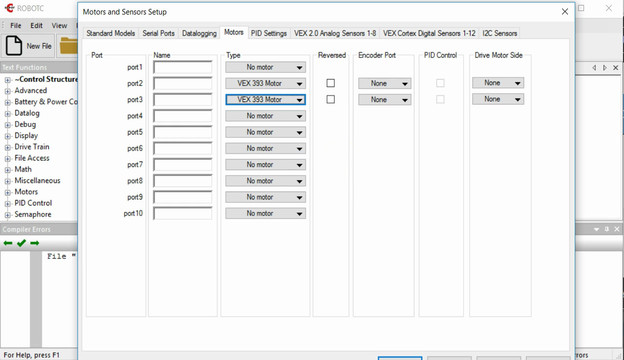
The DcMotor object has support for using encoder counts to control how long the motor will run when turned on. Encoders attach to or are integrated into the drive motors and count the revolutions of the motor shaft either optically or magnetically. A more accurate way to control movement is with encoders. So far we have been controlling the distance the robot travels with elapsed time.
